Gas Turbine Brush Seals
Lower Leakage, Higher Efficiency
Flexible brush seals, made from backward-angled alloy bristles, are immune to rubbing and maintain original clearance longer than labyrinth seals alone, ensuring minimum compressor stage leakage and improved turbine efficiency.
Industrial gas turbines have adopted the brush seal in three primary locations:
- Bearing housing
- High pressure packing (HPP) sealing (compressor section inner barrel sealing)
- Hot gas path interstage sealing
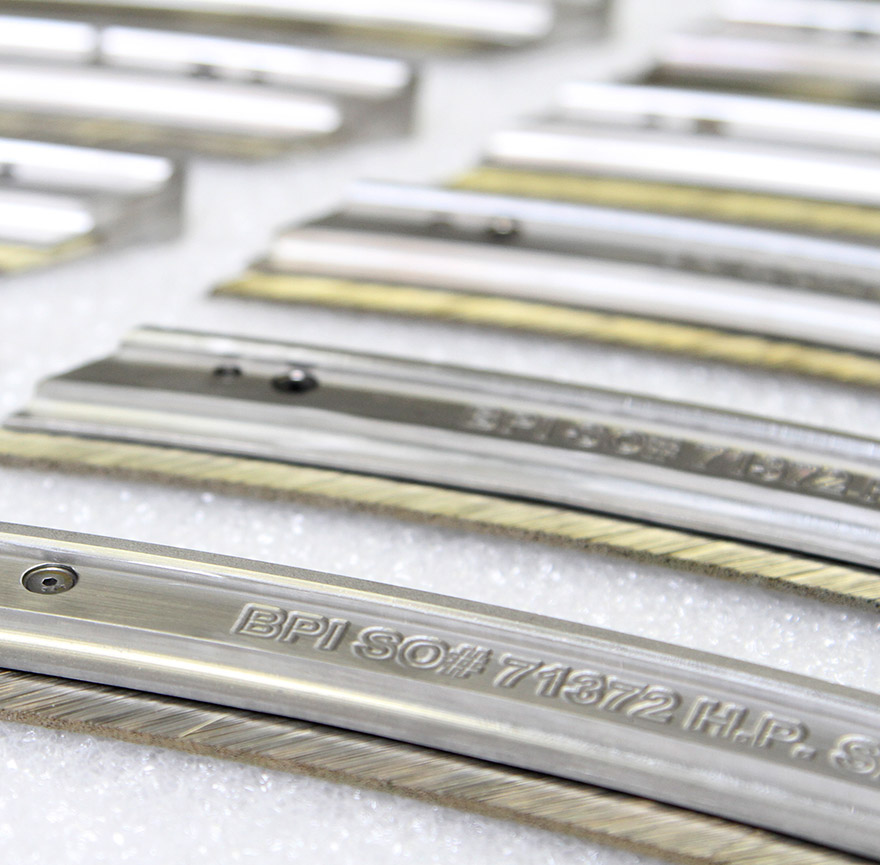
Bearings Plus has provided hundreds of gas turbine brush seals for the most common GE Frame 9, 7, 6, and 5 models and the Westinghouse 501 series.
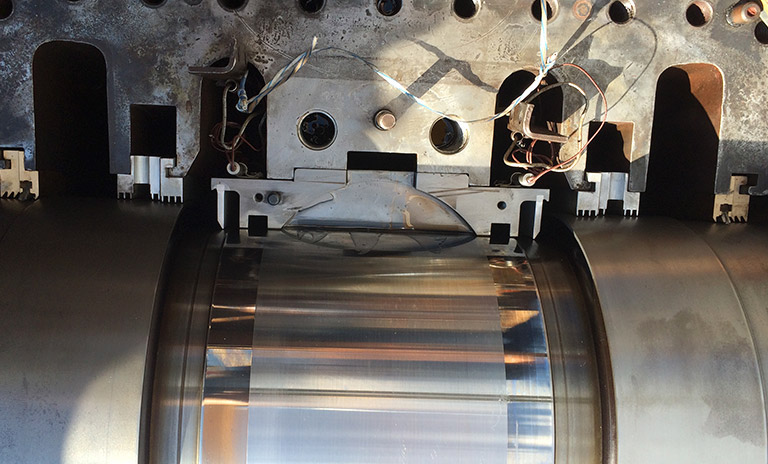
Bearing Housing Brush Seal
On turbines configured with three bearings, the #2 bearing housing seal is a potential leak path of high-pressure air. To minimize compressor air leakage and increase turbine performance, it is possible to retrofit an existing air seal with a modular brush seal, or to retrofit with a complete replacement bronze labyrinth and modular brush seal.
HPP Brush Seal
The inner barrel between a compressor and turbine has high pressure packing (HPP) designed to control the bypass of compressor high-pressure air into the turbine wheel space. Brush seals can supplement labyrinth seals to reduce clearances and cut leakage in half. A complete inner barrel retrofit includes grooving and modular brush seals. OEM brush seal replacements include roll-in single or double hooks to match the OEM design.
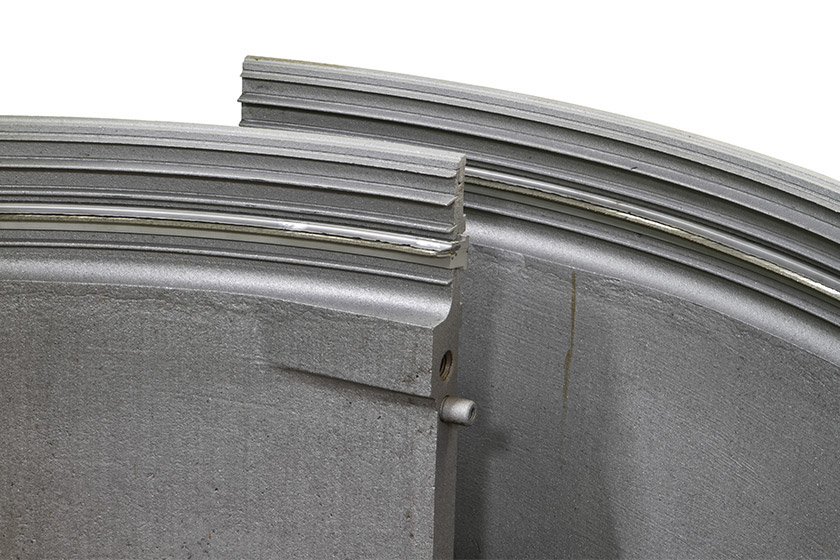
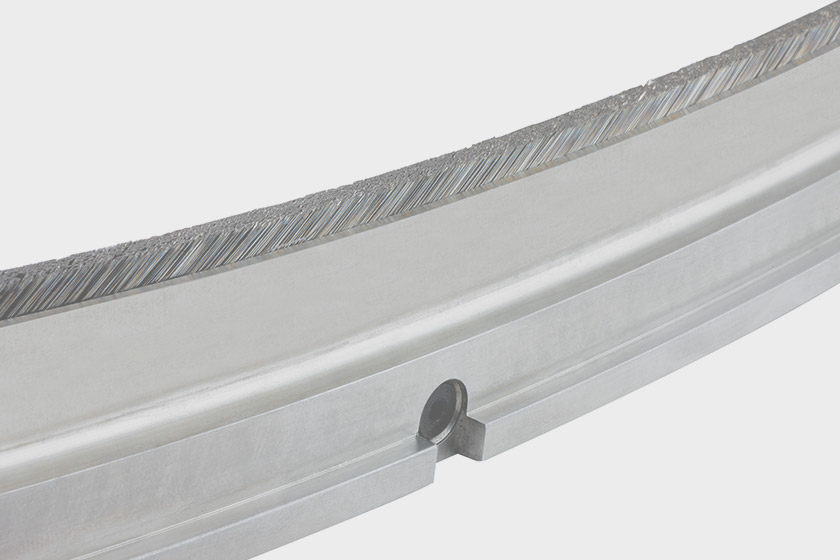
Interstage Brush Seal
On some heavy frame gas turbines, the second stage nozzle/diaphragm assembly contains a radial high-low labyrinth seal designed to reduce leakage between the diaphragm and turbine rotor into the stage 2 forward wheel space area. Replacing the complex high-low labyrinth seal with a simple labyrinth seal augmented with a brush seal can reduce setup time and increase efficiency.
Economical Repair
Over time, as brush seals are subjected to multi-year duty cycles, replacement of the brush seals becomes a requirement. Unlike conventional brush seals, the Bearings Plus modular brush seal assembly has three components: a bristle strip, a top plate, and a back plate.
Our modular assembly allows the replacement of the bristle strip without having to replace the entire seal. Recycling the seal plates and replacing the bristle strip make Bearings Plus brush seals repairable.
Our unique modular assembly can reduce replacement cost by up to 30% when compared to replacement of the entire seal.
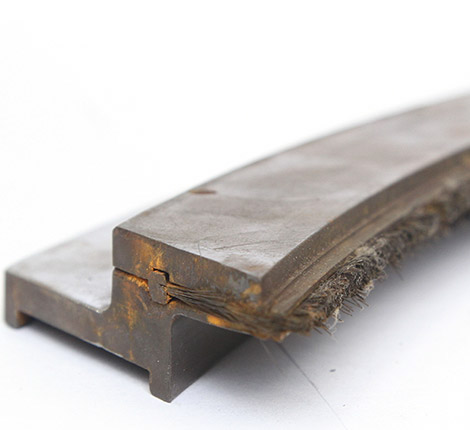
Before Repair
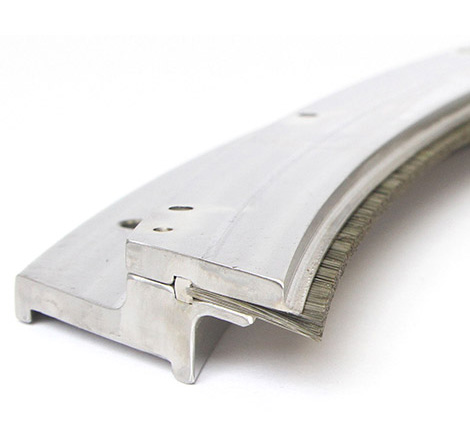
After Repair
Advantages
- Reduce labyrinth bypass air flow by up to 50%
- Increase turbine efficiency by up to 2%
- Minimize shaft bowing and heating caused by rub-in features
- Fit into existing labyrinths, eliminating the need for casing modifications
- Extend time between seal replacements
- Reduce future repair costs with patented modular assembly