Bearing Damage Index
Wiping
A wiped bearing surface is where surface rubbing, melting and smearing is evident. This may be due to a variety of causes, including:
Excessive Load at Start-up/Run-down
Wiping may occur due to excessive load at start-up, run-down or low-speed turning, or barring. The acceptable start-up load depends on the frequency of start-ups and the amount of barring. Please consult a bearing engineer for guidance on acceptable loads.
Addressing the Damage
If the low-speed specific loads exceed acceptable limits and it is not feasible to reduce them, it is advisable to use bearings fitted with a jacking system that uses oil at high pressure injected into special grooves in the bearing to separate the mating surfaces and prevent damage during start-up/run-down.
Alternatively, explore the option of fitting a larger bearing to handle the loads, or using a polymer-lined bearing with improved boundary lubrication properties. Polymer-lined pads can be a simple replacement for babbitt-lined pads, while the installation of hydrostatic jacking may be a significant retrofit.
To determine whether replacement pads or a retrofit bearing with hydrostatic jacking is the most appropriate solution, consult a bearing engineer regarding the machine’s specific operating conditions.
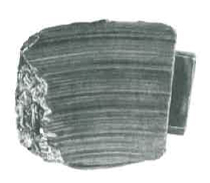
Figure 1: Surface wiping of whitemetal-lined pad in successive thin layers due to excessive steady load at start-up
Insufficient Lubricant
A hydrodynamic, or fluid film, bearing requires an adequate supply of lubricant to be present at start-up for lubrication, during operation for lubrication and heat removal and, sometimes, continuing after shutdown to remove heat that may continue to ‘soak’ from the immediate environment and potentially damage the bearing. A wiped bearing surface may be due to inadequate or interrupted oil supply.
Addressing the Damage
Ensure that the oil supply is adequate and continuous. Consider installing a header tank or back-up pump to prevent interruption of the oil supply during power loss.
In cases of heat soak after shutdown, consider changing to a bearing material with higher temperature capability, such as polymer.
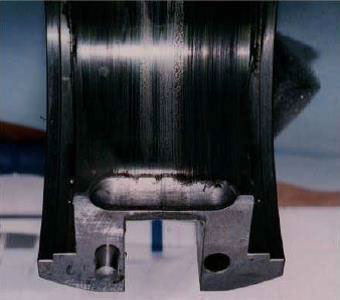
Figure 2: Ring-oiled whitemetal bearing wiped due to oil starvation
Operational Overload
Wiping may follow disruption of the oil film due to extreme operating load or due to shaft vibration that applies a large rotating load to the bearing.
Addressing the Damage
If the steady load is excessive, machine design changes to reduce the load may be required, or consult a bearing engineer for a bearing with a higher load capacity. Within limits it can be possible to make changes to the bearing materials or mechanical designs to increase the hydrodynamic bearing capability within the original space envelope and safely carry an unexpectedly large steady load.
Unexpected dynamic loads, such as an out-of-balance rotor, are inherently difficult for a hydrodynamic bearing to carry without damage. The solution is likely to be removal of the source of the vibration, and the advice of a specialist should be sought.
In general, dynamic loads are unusual in rotating machines with hydrodynamic bearings, which is why babbitt, with its limited fatigue strength, is still often the first choice bearing material. This is changing, however, as machine speeds and/or loads and temperatures increase. Special metallic material combinations and, in particular, polymer materials are available to meet these demands.
Loss of Clearance
Wiping of bearing surfaces can occur due to the use of tight clearances on a machine that has to start up rapidly from cold. Heat generated within the oil film may cause the shaft temperature to rise more rapidly than the bearing housing. Differential expansion of the shaft can cause temporary reduction in the journal bearing clearance, which in severe cases may cause metal-to-metal contact in the zones of minimum clearance in profile bore bearings.
For tilt pad journal bearings, the situation is more severe because the heat flow from pad to housing is particularly poor, causing the pads to expand inwards at start-up.
Addressing the Damage
Consult a bearing engineer for a recommended design clearance to suit operating conditions. If a tight bearing clearance is required to meet a dynamic requirement, the engineer will need to understand whether there is a rapid acceleration to operating speed (e.g., with an electric motor drive) or a slow acceleration (e.g., with a steam turbine drive).
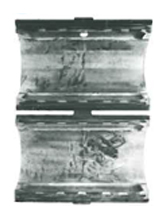
Figure 3: Whitemetal lined turbine bearing, wiped in both top and bottom halves due to inadequate clearance
Misalignment
Another cause of wiped bearing surfaces is misalignment between the shaft and bearing surfaces, which leads to disruption of the oil film at the edge of the bearing and causes a distinctive parabolic-shaped wipe in journal bearings. In thrust bearings, support misalignment can lead to pads at one side being wiped while those on the other side are unmarked.
It may help to understand the effects of misalignment as excessive steady and dynamic loading. A misaligned support casing behind a journal bearing or thrust bearing will cause excessive steady state loading because the full load is falling onto only part of the bearing surface. A rotor running out of true (for example, when out of balance) or a thrust collar running with a swash plate action (the face not being square with the rotor axis) will cause excessive dynamic loading.
Addressing the Damage
If the wipe is slight, the bearing can continue in operation, as its surface will have ‘bedded in’ to the actual shaft alignment and the wipe will stabilize and not get progressively worse. In more severe cases, the bearing will need to be replaced and the alignment of the machine corrected.
If the misalignment changes during machine operation, consult a bearing engineer for a bearing design with some self-alignment capability, such as a tilt pad journal bearing or a equalizing tilt pad thrust bearing.
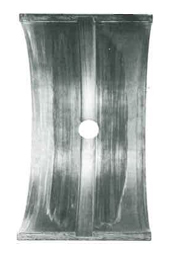
Figure 4: Overlay plated copper bearing wiped due to barrelled shaft